Het ontwerpen van matrijzen voor niet alleen de medische sector vereist unieke benaderingen, en niet alleen Progressive Components heeft exclusieve items waarmee we verschil maken.
Hier volgt een overzicht van items die zijn ontworpen voor maximale prestaties en duurzaamheid van uw kritieke medische gereedschappen:
- Matrijs componenten
- Servo oplossingen
- CLIN behandelde componenten.
Dit bericht is ook als PDF te verkrijgen, geheel onderaan.
A: Standaard Matrijs Componenten
A1: Tapered Date Stamps:

Deze taps toelopende datumstempels hebben een afsluit oppervlak om flash te voorkomen, zelfs bij het gebruik van hoge MFI-kunststoffen zoals LSR, Nylon en Medische-kwaliteit flexibele PVC. Volledig roestvrijstalen constructie, dit gepatenteerde ontwerp heeft geen hoogtevariatie tijdens rotatie.
A2: Medische Matrijs Basis Componenten:
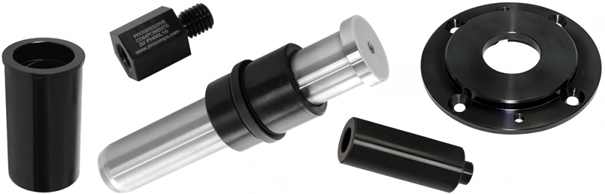
Vetvrij te gebruiken componenten voor medische toepassingen biedt Progressive corrosiebestendige zwart oxide behandelde (Black Nitride) leipennen/bussen en meer.
De BN behandelde leipennen gaan langer mee dan de conventionele.
A3: Soepel Lopende Schuifvergrendelingen:
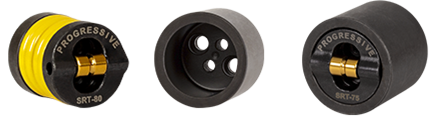
In plaats van constant smeren om metaal-op-metaal slijtage onder schuiven te voorkomen, kunnen de SRT schuif vergrendelingen ingezet worden met geharde 80 HRC Tin gecoate roller schoon en droog draaien, en nu gemakkelijker te installeren in de nieuwe geharde SRT Bus uit 1.2379.
A4: Exclusieve “Black and Gold” Mechanismen
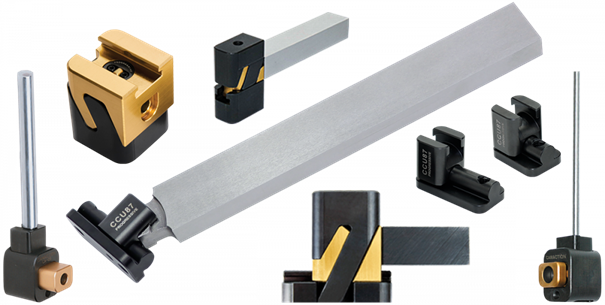
De combinatie van Titanium Nitride (TiN) en Black Nitride (SBN) is onafhankelijk getest en bewezen beter te presteren dan niet alleen look-alike imitaties maar ook DLC vs. DLC.
Dezelfde technologie die bewezen is bestand te zijn tegen de “bump” van het uitlijnen van matrijshelften als gevolg van platen doorzakken is toegepast in standaard CamAction, evenals de smeervrije koppeling van UniLifter U-Coupling en T-Gibs.
Meer achtergrondinformatie over Black Nitride is te vinden bij C: CLIN technologies
A5: Ongeëvenaarde levensduur van de uitlijning
De productlijn matrijs-centrering dekt een groot aantal toepassingen, aangezien holtes en kernen voor medische matrijzen vaak uitlijning van insert naar insert vereisen, en matrijzen soms vrij groot zijn en zwevende platen bevatten. Beginnend met holtevergrendelingen (rond en plat) en interne topvergrendelingen, is uitlijning voor matrijzen tot 34 ton ook mogelijk. Voor meervoudige deellijnen worden de vlakgeleidingslijsten vanaf de zijkant van de matrijs bewerkt.
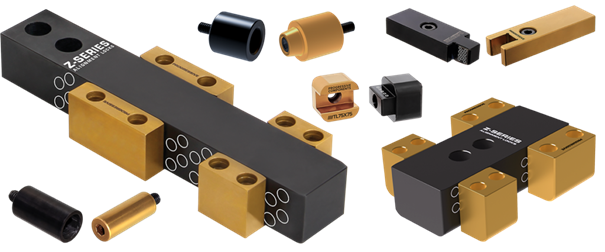
A6: Doorgeharde uitwerp componenten
Black Nitride behandelde pennen vermindert de schade door vreten. Het is bewezen dat vastzittende uitwerppennen minder vaak gerepareerd hoeven te worden. Nauwkeurig gehoonde slepen smeerbaar oppervlak dat geen vet nodig heeft met een hardheid van 66-70 HRC die geschikt is voor zware omstandigheden.

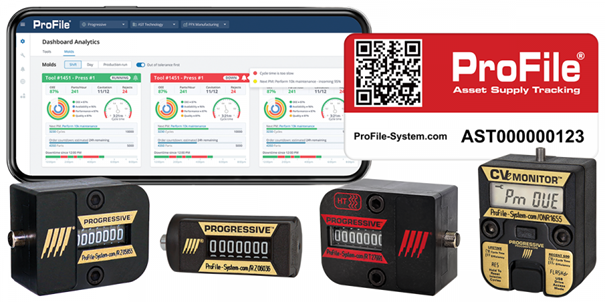
A7: Monitor en Onderhoud
Naast de hierboven genoemde componenten is een extra factor voor medische matrijzen dat ze vaak hogere onderhoudsvereisten hebben.
De CVe-monitoren van Progressive leveren realtime gegevens en ProFile® biedt veilige toegang op afstand voor het beheer van door de gebruiker gedefinieerde onderhoudsintervallen voor matrijzen, machines en apparatuur, en nog veel meer.
B: Servo systemen voor veilige en schone producten
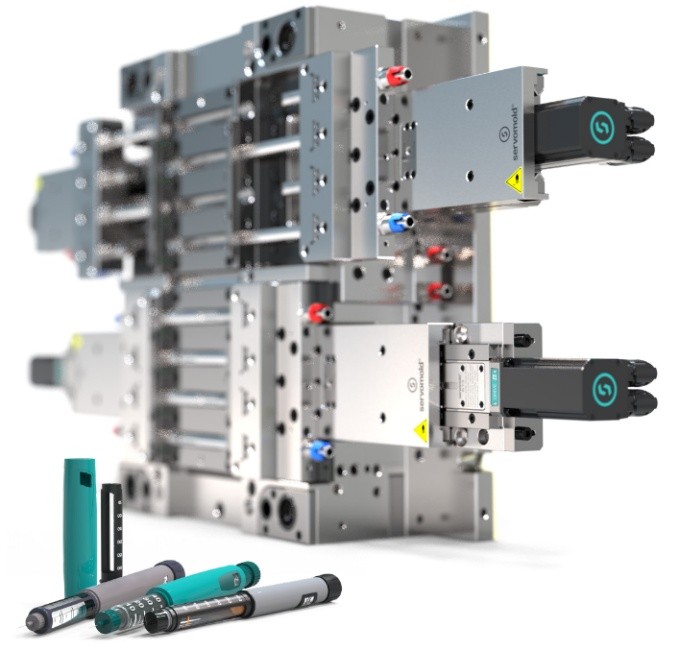
Honderd procent reinheid en braamvrije verwerking zijn vereist voor kunststof componenten in de medische en farmaceutische sector om de veiligheid van de patiënt en een soepele werking te garanderen. De systeemoplossingen van Servomold creëren ideale omstandigheden voor cleanroom productie met uitgebreide controle, traceerbaarheid en documentatie van alle procesparameters.
- Individuele systemen volgens toepassing en procesvereisten
- Efficiënte aandrijf- en tandwielsystemen verkorten cyclustijden
- 100% positioneer- en herhalingsnauwkeurigheid in alle processen
- Permanente bewaking van alle procesinformatie mogelijk
- Kan compact worden geïntegreerd in alle standaard spuitgietmachines
- Olievrij en schoon, geschikt voor cleanroom klasse ISO7 / GMP-C / 10.000
Het spuitgietgereedschap in zowel de medische en farmaceutische sector enz. vereist een speciale mate van precisie, netheid en procesbeheersing.
B1: Hoe servotechnologie de hoge eisen overtreft
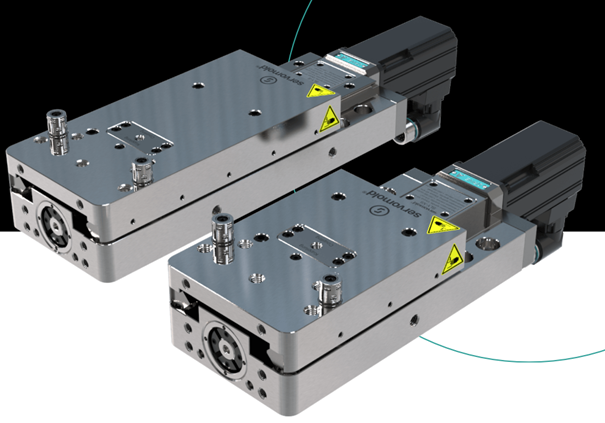
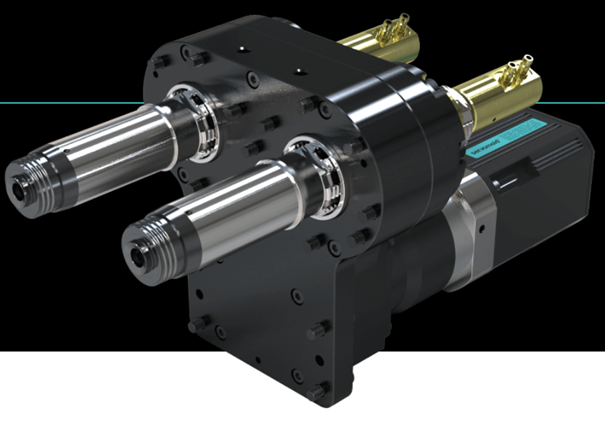
Kleine onzuiverheden, grote ramp. Bij de productie van farmaceutische primaire verpakkingen of medische kunststof onderdelen zoals zeer nauwkeurige Luer lock-systemen, is reinheid voor de machine, de matrijs en het spuitgietproduct geen formaliteit, maar een streng gereguleerde productienorm, waarvan de naleving bepalend is voor de kwaliteit van hele batches. Niemand wil dat er duizenden onderdelen voor niets worden geproduceerd vanwege vervuiling op de schroefdop. Servo-elektrische automatiseringsconcepten voeren niet alleen op betrouwbare wijze translerende en lineaire bewegingen uit, ze minimaliseren ook het risico op vervuiling. Maar wat is precies de technologie erachter? Laten we de servo voordelen eens onder de loep nemen.
B2: De optimale oplossing voor de hoge cleanroom klassen
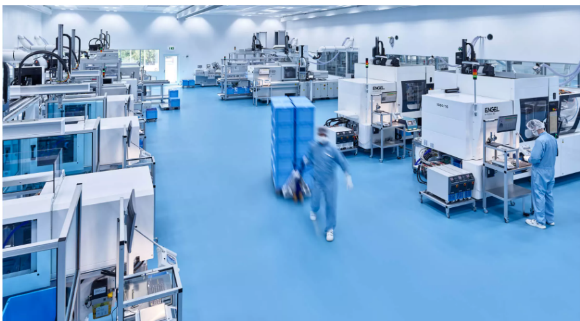
Bij spuitgietmachines in cleanrooms gaat de trend al enkele jaren duidelijk in de richting van volledig elektrische machines. Als borstel- en ventilator loze motoren zijn servomotoren volledig schoon, energiezuinig met minimaal warmteverlies en zonder uitstoot van deeltjes. De smeermiddelarme technologie is daarom ideaal voor cleanrooms tot klasse ISO7 / GMP-C / 10.000.
De significante vermindering of zelfs eliminatie van smeermiddelen in spuitgietmatrijzen helpt ook om het risico op vervuiling te verminderen – dit vereist echter dat bewegingen met grotere precisie en controleerbaarheid worden uitgevoerd – dit aspect kan ook eenvoudig worden bereikt met servomotoren.
B3: Waar hoge kwaliteit vereist is, worden de sterke punten duidelijk.
Naast het vrij zijn van vervuiling behoren ook de uitstekende precisie en productiekwaliteit tot de belangrijkste kenmerken binnen een cleanroom productie. De basis hiervoor wordt geleverd door systemen waarmee productieprocessen en matrijsbewegingen tot in detail kunnen worden uitgelijnd en herhaald.
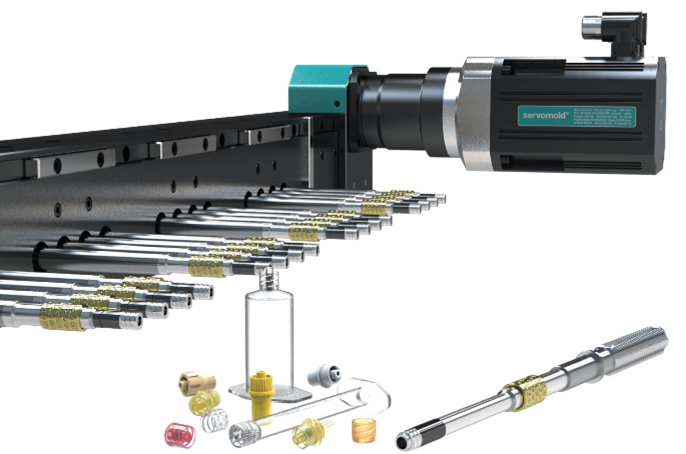
Een belangrijk aspect is bijvoorbeeld de vereiste afwezigheid van bramen aan kunststof onderdelen die later in contact komen met bloed – zo moet b.v. de matrijzen voor Luer lock-systemen geproduceerd worden met zeer lage toleranties en extreem smalle openingen. In combinatie met de vereiste vrijheid van smeermiddelen en zeer dynamische bewegingen voor korte cyclustijden, creëert dit een situatie die moeilijk te beheersen en te controleren is met hydraulische systemen.
Servoaandrijvingen kunnen gevoelig en nauwkeurig worden geregeld met behulp van de positie-encoder die op de servomotor is geïnstalleerd, zoals een elektromagnetische resolver of opto-elektronische absolute encoder. Afhankelijk van het systeem wordt één omwenteling van de motoras van een servomotor omgezet in honderden tot duizenden pulsen – de servo-regelaar in het servobesturingssysteem gebruikt deze signalen om de servomotor nauwkeurig te besturen met een nauwkeurigheid van enkele hoekminuten. Dit betekent dat mechanismen kunnen worden gepositioneerd met een nauwkeurigheid van 1/100ste van een millimeter zonder dat een eindstop nodig is. Koppel, krachten en snelheden kunnen worden begrensd en permanent bewaakt, en elk type versnelling kan worden gerealiseerd. Het resultaat is dat servo technologie de mechanische belasting vermindert, het risico op schade aanzienlijk verkleint en de levensduur van de spuitgietmatrijs verlengt.
B4: Controleerbare kwaliteit en stabiele processen
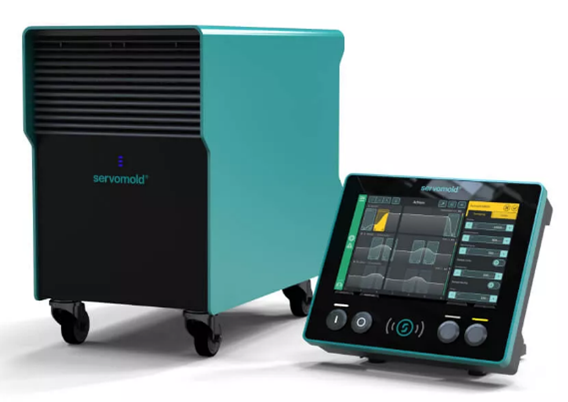
Een servomotor beweegt geen millimeter zonder de juiste servobesturing – deze vereiste is ook de grootste kracht van servo technologie. Moderne servobesturingen bieden niet alleen volledige controle over bewegingen, ze maken ook de registratie van relevante procesparameters mogelijk en dragen zo bij aan de continue bewaking van de productkwaliteit.
Door het koppel en de temperatuur van de servomotor te analyseren, kunnen direct conclusies worden getrokken over de consistentie van de bewegingsvolgorde en kan dus belangrijke informatie worden verkregen bij procesafwijkingen. Veranderingen of zelfs slijtage aan de spuitgietmatrijs kunnen in een vroeg stadium worden gedetecteerd en er kunnen gerichte maatregelen worden genomen.
Materiaal- of parameter gerelateerde veranderingen in het spuitgietproces worden ook zichtbaar – verschillende injectiedrukken worden bijvoorbeeld merkbaar door de verandering in ontvormkrachten. Hier biedt de procesbewaking van de servobesturing ideale mogelijkheden om stabiele en controleerbare processen te garanderen.
B5: Een troef achter de hand met servotechnologie
De energieprijzen hebben een recordhoogte bereikt, productiefaciliteiten komen onder druk te staan en het einde is nauwelijks in zicht. Maar als het om energie-efficiëntie gaat, presteert servo technologie beter dan al haar concurrenten. Vergeleken met hydraulische systemen verbruikt servo technologie vier keer minder energie en zelfs een factor tien bij pneumatische systemen.
C: CLIN™ Technologies Liquid nitrocarburizing treatments
Zoutbad nitrering biedt aanzienlijke verbeteringen op het gebied van wrijving, corrosiebescherming, weerstand tegen vermoeiing, abrasieve en adhesieve slijtvastheid (vastlopen).
C1: CLIN™-behandelingsrichtlijnen:
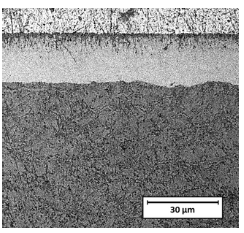
Nitrocarboneer behandelingen zijn thermochemische processen die diffusie van de elementen stikstof en koolstof in het substraat mogelijk maken.
Op micro structurele schaal creëert deze diffusie twee lagen:
- Een combinatielaag in het oppervlak, voornamelijk samengesteld uit ijzernitriden;
- Een diepere diffusielaag waar de elementen (N en C) zich bevinden geïntercaleerd in het materiaal, waardoor een hardheidsgradiënt ontstaat.
CLIN™-processen combineren deze stap met een post-oxidatie en impregnatie:
- Tijdens de oxidatiefase ontstaat er een laag ijzeroxide (Fe₃O₄) die als een passieve film fungeert en de corrosieweerstand verbetert.
- Bij de impregnatiestap wordt gebruik gemaakt van de microporiën die tijdens de behandeling ontstaan om organische verbindingen vast te houden. Dit verbetert de corrosieweerstand en het wrijvingsgedrag aanzienlijk.
De combinatie van deze vloeibare nitrocarboneer stappen resulteert in meerdere kenmerken, waardoor processen zoals ARCOR™ doeltreffende en veelzijdige behandelingen opleveren.
C2: ARCOR™: een flexibel assortiment industriële behandelingen.
Ontwikkeld om te voldoen aan de eisen en problemen van de klant (technisch, economisch en ecologisch).
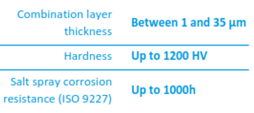
ARCOR™ procesparameters zijn instelbaar om de gewenste prestaties te bereiken.
CLIN™: Een reeks robuuste en reproduceerbare processen:
- Snelle verwerking (minder dan 3 uur) en gefaseerde koeling om vervorming te beperken.
- Mogelijkheid om onderdelen met complexe vormen te bewerken.
- De homogeniteit van de vloeistofomgeving zorgt voor een uniforme behandeling over de volledige lading.
- Behandeld in dezelfde omgeving zijn de kenmerken van de onderdelen reproduceerbaar van batch tot batch
C3: Technologie op maat
CLIN-processen worden uitgevoerd op afgewerkte onderdelen en profiteren van afwerking op maat.
Voorbeelden:
- Mechanische behandeling (tribofinishing, polijsten, enz.) kan worden toegepast om de oppervlaktekwaliteit te optimaliseren.
- Toevoeging van een lak om de weerstand van onderdelen tegen passingsroest verder te verbeteren.
C4: Milieueffecten
Bij CLIN™-processen komen geen VOS of NOx vrij en er worden geen PFAS-stoffen gebruikt.
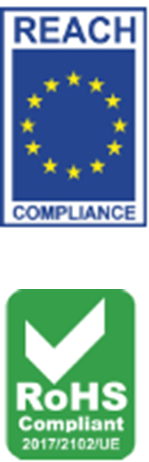
De HEF Group heeft het ECO-CLIN™ proces ontwikkeld en gepatenteerd, een innovatie die het mogelijk maakt om procesafval te recyclen en om te zetten in nieuwe verbruiksgoederen die direct kunnen worden gebruikt in de lijn.
CLIN™ technologieën maken deel uit van een circulair economisch model:
- Minder impact op natuurlijke hulpbronnen
- Zorgen voor een veilige aanvoer van grondstoffen
- Naleving van regelgeving en hierop anticiperen
De voordelen van CLIN™ technologieën: concurrerende ten opzichte van elektrolytisch vernikkelen, hardverchromen en zelfs gasnitreren.
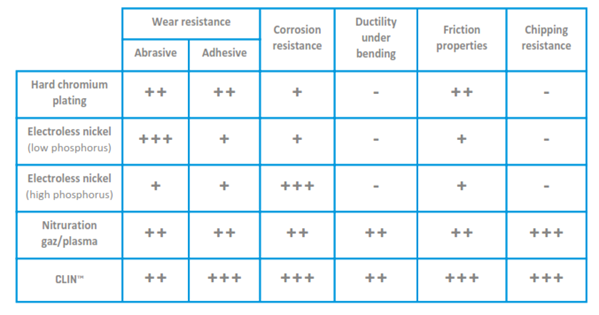